Brazing is a versatile joining process that relies on heat to melt a filler metal, which then flows into the joint by capillary action. The source of heat for brazing varies depending on the specific method used, which is chosen based on factors such as the materials being joined, joint geometry, production volume, and desired quality. Common heating methods include torch brazing, furnace brazing, induction brazing, dip brazing, resistance brazing, and advanced techniques like electron beam and laser brazing. Each method has unique advantages and is suited to specific applications, ensuring efficient heat transfer and precise control over the brazing process.
Key Points Explained:
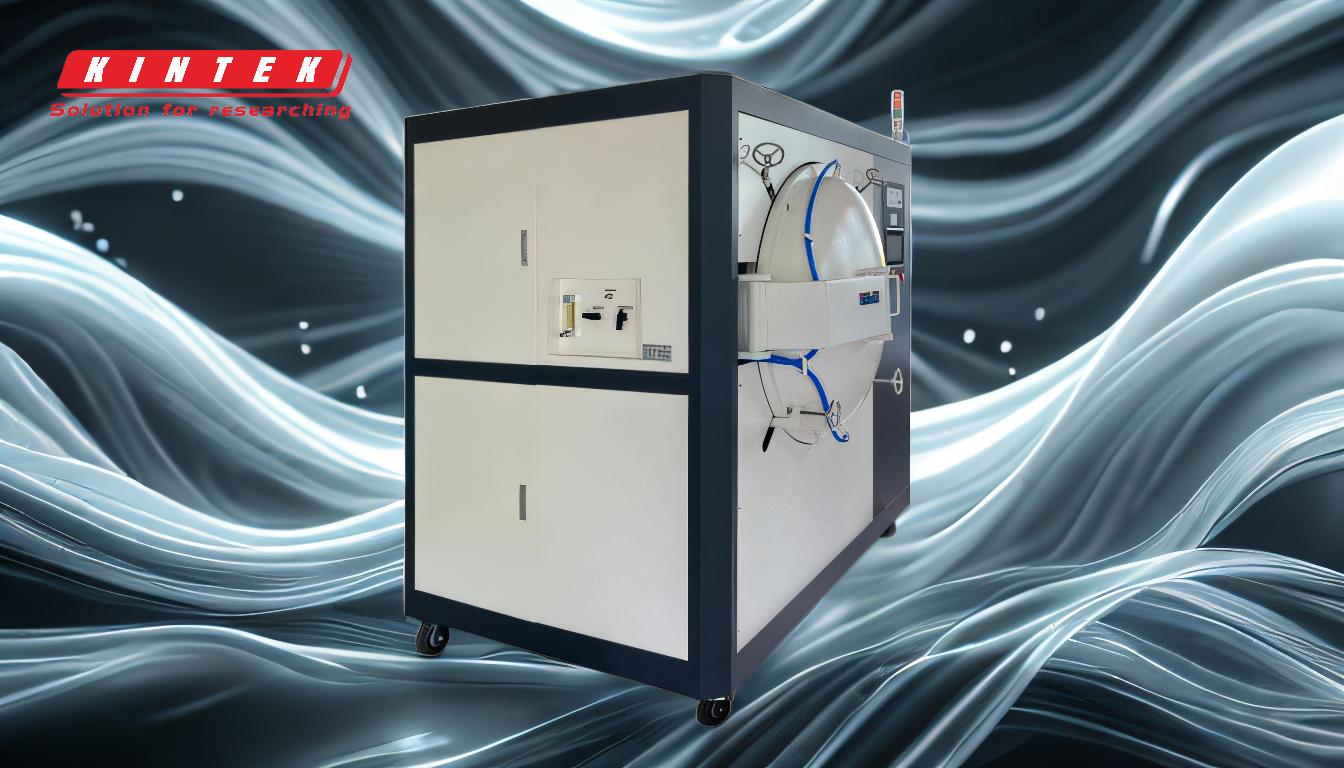
-
Torch Brazing:
- Torch brazing uses a gas flame as the heat source, typically fueled by oxy-acetylene, propane, or natural gas.
- This method is highly versatile and portable, making it suitable for small-scale or on-site repairs.
- It allows precise control over the heat application, which is ideal for localized heating of joints.
-
Furnace Brazing:
- Furnace brazing involves heating the entire assembly in a controlled environment, such as exothermic, hydrogen, argon, or vacuum atmospheres.
- This method is ideal for high-volume production and complex assemblies, as it ensures uniform heating and minimizes oxidation.
- The controlled atmosphere prevents contamination and ensures high-quality joints.
-
Induction Brazing:
- Induction brazing uses electromagnetic induction to generate heat within the workpiece itself, through the Joule effect.
- This method is highly efficient and provides rapid, localized heating, making it suitable for precise and repeatable brazing operations.
- It is commonly used for joining conductive materials like stainless steel.
-
Dip Brazing:
- Dip brazing involves immersing the assembly in a molten salt or metal bath, which acts as both the heat source and the filler material.
- This method is effective for large-scale production and ensures uniform heating of complex geometries.
- It is particularly useful for materials that are difficult to heat evenly using other methods.
-
Resistance Brazing:
- Resistance brazing uses electrical resistance to generate heat at the joint interface.
- This method is ideal for small, localized joints and provides precise control over the heat application.
- It is commonly used in electronics and other industries where minimal heat distortion is critical.
-
Infrared Brazing:
- Infrared brazing uses focused infrared radiation to heat the joint area.
- This method is suitable for materials that require precise temperature control and minimal heat-affected zones.
- It is often used in applications where contamination must be avoided.
-
Advanced Methods:
- Electron Beam and Laser Brazing: These methods use highly focused energy beams to achieve precise and localized heating. They are ideal for high-precision applications and materials that are sensitive to heat.
- Blanket Brazing: This method uses flexible heating blankets to provide uniform heat to large or irregularly shaped components.
-
Factors Influencing Heat Source Selection:
- Efficient Heat Transfer: The chosen method must ensure even heat distribution across the joint.
- Heat Capacity of Base Metals: The method must not exceed the thermal limits of the materials being joined.
- Joint Geometry: Complex geometries may require specialized heating methods.
- Production Rate and Volume: High-volume production often favors methods like furnace or dip brazing.
By understanding these key points, equipment and consumable purchasers can make informed decisions about the most suitable brazing methods and heat sources for their specific applications.
Summary Table:
Brazing Method | Heat Source | Key Advantages |
---|---|---|
Torch Brazing | Gas flame (oxy-acetylene, propane, etc.) | Versatile, portable, precise control for localized heating. |
Furnace Brazing | Controlled environment (exothermic, vacuum) | Uniform heating, ideal for high-volume production, prevents oxidation. |
Induction Brazing | Electromagnetic induction | Rapid, localized heating, efficient for conductive materials like stainless steel. |
Dip Brazing | Molten salt or metal bath | Uniform heating for complex geometries, suitable for large-scale production. |
Resistance Brazing | Electrical resistance | Precise control, minimal heat distortion, ideal for electronics. |
Infrared Brazing | Focused infrared radiation | Precise temperature control, minimal heat-affected zones, avoids contamination. |
Advanced Methods | Electron beam, laser, or heating blankets | High precision, localized heating, ideal for sensitive materials or large parts. |
Need help choosing the right brazing method for your project? Contact our experts today for personalized guidance!