A resistive heating element works by converting electrical energy into heat through a process known as Joule heating or resistive heating. When an electric current passes through the heating element, the material's resistance to the flow of electrons causes collisions between electrons and atoms, transferring kinetic energy as heat. This process is governed by the I²R effect, where heat generation is proportional to the square of the current and the resistance of the material. Heating elements are designed using materials like metallic alloys, ceramics, or ceramic metals, which provide the right balance of resistance and durability to produce the required heat without melting or degrading.
Key Points Explained:
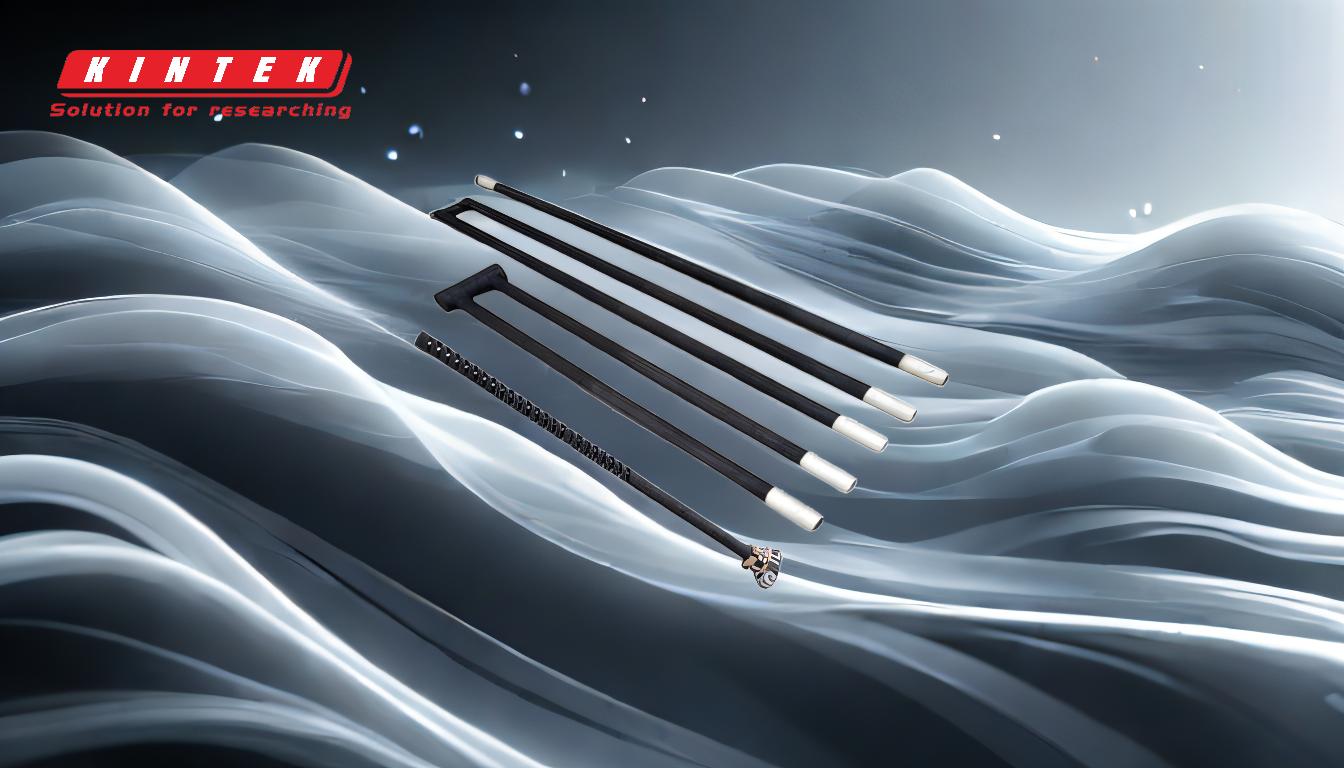
-
Joule Heating Principle:
- Resistive heating elements operate on the principle of Joule heating, where electrical energy is converted into heat as current flows through a resistive material.
- The heat generated is proportional to the square of the current (I²) and the resistance (R) of the material, as described by the formula ( P = I^2R ), where ( P ) is power (heat) in watts.
-
Role of Resistance:
- The heating element's material resists the flow of electricity, causing electrons to collide with atoms in the material.
- These collisions transfer kinetic energy to the atoms, increasing their vibrational energy, which manifests as heat.
- The resistance of the material is carefully chosen to ensure optimal heat generation without causing the material to fail.
-
Material Selection:
- Heating elements are made from materials that provide the right balance of electrical resistance and thermal stability.
- Common materials include:
- Metallic Alloys: Such as nichrome (nickel-chromium), which offers high resistance and oxidation resistance at high temperatures.
- Ceramics: Used for their high melting points and thermal stability.
- Ceramic Metals (Cermets): Combine the properties of metals and ceramics for specialized applications.
- The material must withstand high temperatures without melting, oxidizing, or degrading.
-
Design Considerations:
- The cross-sectional area and length of the heating element are designed to provide the desired resistance and heat output.
- Thinner or longer elements increase resistance, while thicker or shorter elements decrease resistance.
- The goal is to achieve the required heat output while ensuring the element operates safely within its temperature limits.
-
Direction Independence:
- Unlike the Peltier effect, which depends on the direction of current flow, Joule heating is independent of current direction.
- This makes resistive heating elements suitable for both alternating current (AC) and direct current (DC) applications.
-
Applications:
- Resistive heating elements are widely used in:
- Household Appliances: Such as toasters, ovens, and water heaters.
- Industrial Furnaces: For processes requiring high-temperature heating.
- Electric Heaters: Including space heaters and industrial heating systems.
- Their versatility and reliability make them a cornerstone of modern heating technology.
- Resistive heating elements are widely used in:
-
Insulation and Efficiency:
- In applications like insulation-lined furnaces, the heating element is surrounded by insulating materials to minimize heat loss and improve energy efficiency.
- Proper insulation ensures that the generated heat is directed toward the intended target, reducing waste and improving performance.
By understanding these key points, a purchaser can make informed decisions about selecting the appropriate resistive heating elements for their specific needs, ensuring optimal performance, durability, and energy efficiency.
Summary Table:
Key Aspect | Description |
---|---|
Joule Heating Principle | Heat is generated as current flows through a resistive material (P = I²R). |
Role of Resistance | Resistance causes electron-atom collisions, converting kinetic energy into heat. |
Material Selection | Materials like nichrome, ceramics, and cermets balance resistance and stability. |
Design Considerations | Length and cross-sectional area are optimized for desired heat output. |
Direction Independence | Works with both AC and DC, independent of current direction. |
Applications | Used in household appliances, industrial furnaces, and electric heaters. |
Insulation & Efficiency | Insulating materials minimize heat loss and improve energy efficiency. |
Ready to optimize your heating solutions? Contact our experts today for tailored advice!