Induction heating is a process that relies on generating heat within a conductive material by exposing it to a varying electromagnetic field. The efficiency and effectiveness of this process depend on several key factors, including the frequency of the electric current, the size and material of the object being heated, the coupling between the work coil and the object, and the penetration depth of the electromagnetic field. Understanding these dependencies is crucial for optimizing induction heating systems for various applications.
Key Points Explained:
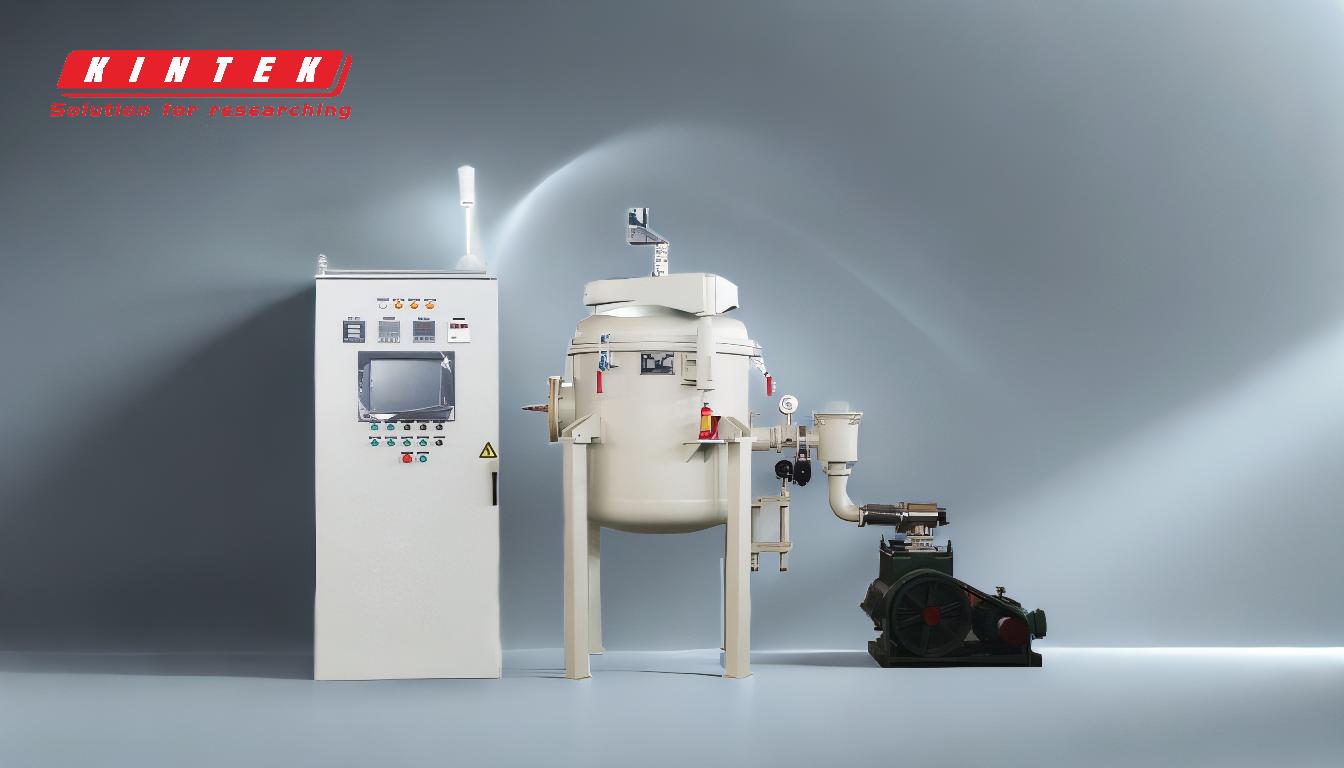
-
Frequency of the Electric Current:
- The frequency of the alternating current (AC) used in induction heating is a critical factor. Higher frequencies are generally used for smaller objects or for heating thin layers, while lower frequencies are suitable for larger objects or deeper penetration.
- The choice of frequency affects the skin depth, which is the depth at which the current density falls to about 37% of its value at the surface. Higher frequencies result in a shallower skin depth, concentrating the heating effect near the surface.
-
Object Size:
- The size of the object being heated influences the choice of frequency. Larger objects require lower frequencies to achieve sufficient penetration depth, ensuring that the heat is distributed throughout the material.
- Smaller objects can be effectively heated with higher frequencies, as the heat needs to penetrate a smaller volume.
-
Material Type:
- The electrical conductivity and magnetic permeability of the material being heated play a significant role in induction heating. Materials with high electrical conductivity, such as copper and aluminum, heat up more efficiently.
- Magnetic materials, like iron and steel, heat more effectively due to both resistive heating (from eddy currents) and hysteresis losses (from the magnetic domains aligning with the alternating field).
-
Coupling Between the Work Coil and the Object:
- The efficiency of induction heating is highly dependent on the coupling between the work coil (inductor) and the object being heated. Good coupling ensures that the maximum amount of electromagnetic energy is transferred to the object.
- Factors affecting coupling include the distance between the coil and the object, the shape of the coil, and the alignment of the coil with the object.
-
Penetration Depth:
- Penetration depth, or skin depth, is the distance from the surface of the material at which the current density decreases to about 37% of its surface value. It is inversely proportional to the square root of the frequency, material conductivity, and permeability.
- For effective heating, the penetration depth should be appropriate for the thickness of the material being heated. Too shallow a penetration depth may result in uneven heating, while too deep a penetration may lead to excessive energy consumption.
By carefully considering these factors, induction heating systems can be optimized for specific applications, ensuring efficient and effective heating of materials.
Summary Table:
Factor | Description |
---|---|
Frequency | Higher frequencies for small objects; lower frequencies for larger objects. |
Object Size | Larger objects require lower frequencies; smaller objects use higher frequencies. |
Material Type | High conductivity and magnetic permeability enhance heating efficiency. |
Coupling | Good coupling ensures maximum energy transfer between coil and object. |
Penetration Depth | Appropriate depth ensures even heating; too shallow or deep causes inefficiency. |
Optimize your induction heating system today—contact our experts for tailored solutions!