The heating rate in heat treatment significantly influences the microstructure, mechanical properties, and overall performance of materials. A faster heating rate can lead to thermal gradients, uneven phase transformations, and potential stress buildup, while a slower rate ensures uniform heating, minimizes distortion, and allows for controlled phase transformations. The choice of heating rate depends on the material type, desired properties, and the specific heat treatment process being employed. Balancing speed and uniformity is critical to achieving optimal results.
Key Points Explained:
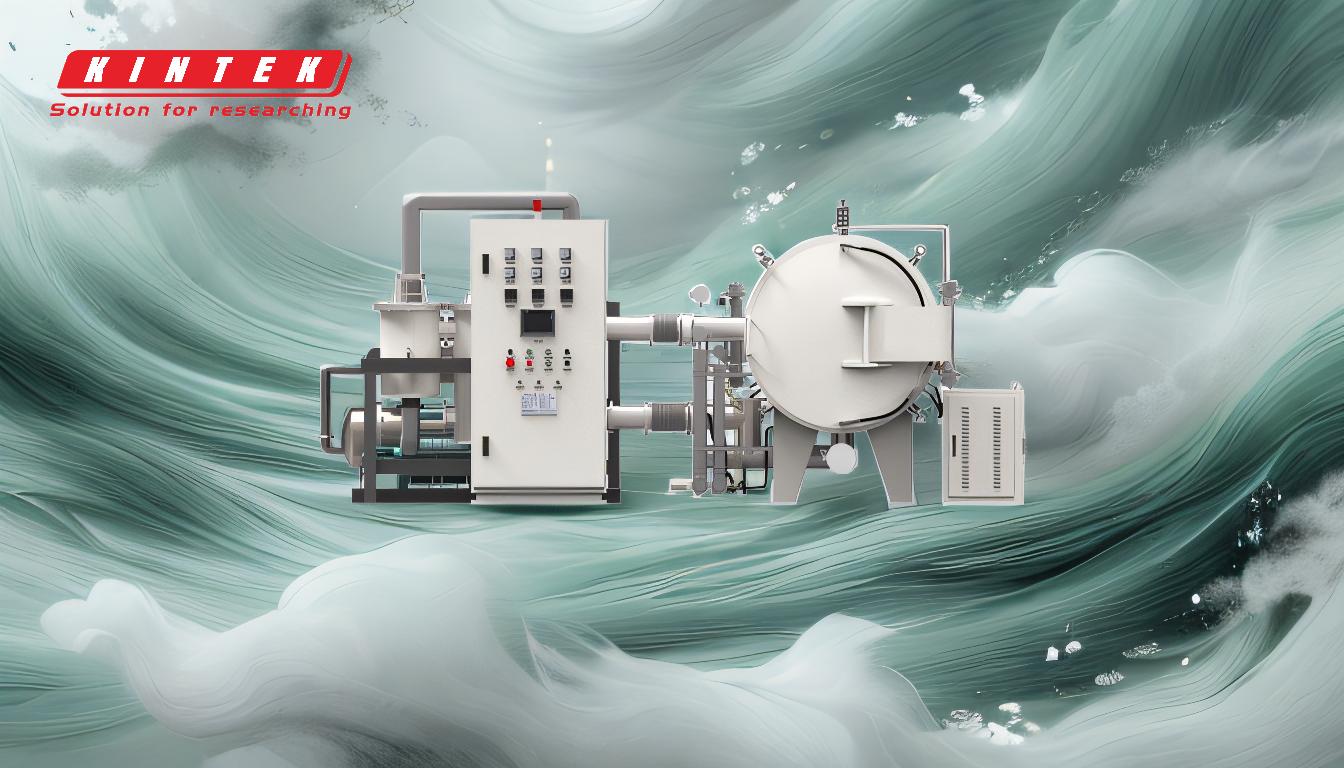
-
Impact on Microstructure:
- Faster Heating Rates: Can result in uneven heating, leading to localized thermal gradients. This may cause non-uniform phase transformations, such as incomplete austenitization in steels, which can negatively affect hardness and strength.
- Slower Heating Rates: Allow for uniform heat distribution, ensuring consistent phase transformations. This is particularly important for achieving homogeneous microstructures, such as fully tempered martensite or spheroidized carbides.
-
Thermal Stress and Distortion:
- Faster Heating Rates: Increase the risk of thermal stress due to rapid expansion and contraction. This can lead to warping, cracking, or residual stresses in the material.
- Slower Heating Rates: Minimize thermal gradients, reducing the likelihood of distortion and stress-related defects. This is especially critical for complex geometries or thin-walled components.
-
Phase Transformation Control:
- Faster Heating Rates: May result in incomplete or delayed phase transformations, particularly in materials with high hardenability. For example, in steels, rapid heating might not allow sufficient time for carbon diffusion, leading to inhomogeneous austenite formation.
- Slower Heating Rates: Provide adequate time for diffusion-controlled processes, ensuring complete and uniform phase transformations. This is essential for achieving desired mechanical properties, such as toughness and ductility.
-
Energy Efficiency and Process Time:
- Faster Heating Rates: Reduce overall process time, which can be beneficial for high-throughput manufacturing. However, they may require higher energy input and more sophisticated equipment to manage thermal gradients.
- Slower Heating Rates: Increase process time but are often more energy-efficient and easier to control. They are typically preferred for critical applications where material integrity is paramount.
-
Material-Specific Considerations:
- Steels: The heating rate must be carefully controlled to avoid cracking or distortion, especially in high-carbon or alloy steels. Slow heating is often recommended to ensure uniform austenitization.
- Aluminum Alloys: Faster heating rates can be tolerated due to their high thermal conductivity, but care must still be taken to avoid overheating or localized melting.
- Titanium Alloys: Require precise heating rates to avoid beta phase embrittlement or unwanted phase transformations.
-
Equipment and Process Design:
- Faster Heating Rates: May necessitate advanced heating systems, such as induction or laser heating, to achieve rapid and controlled temperature changes.
- Slower Heating Rates: Can be achieved with conventional furnaces, making them more accessible and cost-effective for many applications.
-
Practical Implications for Purchasers:
- When selecting heat treatment equipment, consider the heating rate capabilities and their alignment with the materials and components being processed.
- For high-precision applications, prioritize equipment that offers precise control over heating rates to ensure consistent results.
- Evaluate the trade-offs between process speed and material performance to determine the optimal heating rate for your specific needs.
By understanding the effects of heating rate, purchasers can make informed decisions about heat treatment processes and equipment, ensuring that the desired material properties are achieved efficiently and reliably.
Summary Table:
Aspect | Faster Heating Rates | Slower Heating Rates |
---|---|---|
Microstructure | Uneven heating, localized thermal gradients, non-uniform phase transformations. | Uniform heat distribution, consistent phase transformations, homogeneous microstructures. |
Thermal Stress | Higher risk of thermal stress, warping, cracking, or residual stresses. | Minimized thermal gradients, reduced distortion, and stress-related defects. |
Phase Transformation | Incomplete or delayed phase transformations, inhomogeneous austenite formation. | Complete and uniform phase transformations, ensuring desired mechanical properties. |
Energy Efficiency | Reduced process time but higher energy input and advanced equipment required. | Longer process time but more energy-efficient and easier to control. |
Material-Specific Needs | Steels: Risk of cracking; Aluminum: Tolerable; Titanium: Risk of embrittlement. | Steels: Uniform austenitization; Aluminum: Avoid overheating; Titanium: Precise control. |
Equipment | Requires advanced systems like induction or laser heating. | Achievable with conventional furnaces, cost-effective. |
Ready to optimize your heat treatment process? Contact our experts today for tailored solutions!