The tightness rate of a leak refers to the measurement of how effectively a system or component prevents the escape or entry of fluids (liquids or gases) under specific conditions. It is a critical parameter in industries where containment is essential, such as in pipelines, storage tanks, or HVAC systems. The tightness rate is often expressed as a percentage or a specific leakage rate (e.g., volume per unit time). A higher tightness rate indicates better sealing performance, while a lower rate suggests potential leakage issues. Understanding and measuring the tightness rate helps ensure system integrity, safety, and efficiency.
Key Points Explained:
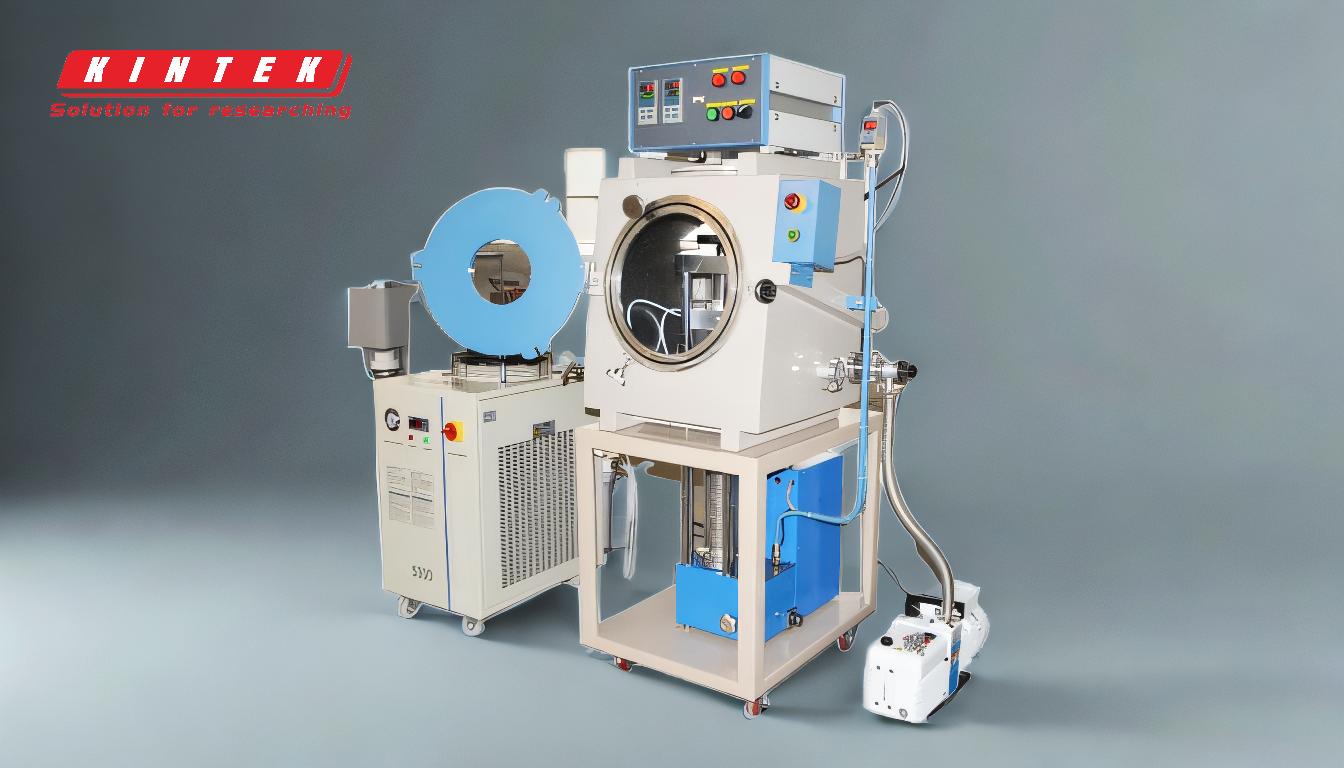
-
Definition of Tightness Rate:
- The tightness rate quantifies the ability of a system or component to prevent leaks. It is a measure of how well a seal or barrier performs under pressure or vacuum conditions.
- It is often expressed as a percentage, where 100% indicates no leakage, or as a leakage rate (e.g., liters per minute or cubic meters per hour).
-
Importance in Industry:
- In industries like oil and gas, pharmaceuticals, and HVAC, maintaining a high tightness rate is crucial for safety, environmental protection, and operational efficiency.
- Leaks can lead to product loss, contamination, or hazardous situations, making tightness testing a standard practice during installation and maintenance.
-
Measurement Methods:
- Pressure Decay Testing: Measures the drop in pressure over time to determine leakage. A slower pressure drop indicates a higher tightness rate.
- Vacuum Testing: Similar to pressure decay testing but performed under vacuum conditions to detect leaks.
- Bubble Testing: Submerging the system in water and observing bubbles to identify leaks. This method is less precise but useful for small-scale applications.
- Tracer Gas Testing: Uses gases like helium to detect leaks with high sensitivity, often used in critical systems.
-
Factors Affecting Tightness Rate:
- Material Quality: The integrity of seals, gaskets, and welds directly impacts tightness.
- Design and Assembly: Proper design and assembly techniques minimize potential leakage points.
- Operating Conditions: Temperature, pressure, and fluid properties can influence the tightness rate over time.
-
Standards and Regulations:
- Many industries follow specific standards (e.g., ISO, ASME) to define acceptable tightness rates and testing procedures.
- Compliance with these standards ensures system reliability and safety.
-
Applications:
- Pipelines: Tightness testing ensures no leaks in oil, gas, or water pipelines, preventing environmental damage and financial losses.
- Storage Tanks: High tightness rates are essential for storing hazardous or volatile materials.
- HVAC Systems: Ensures efficient operation and prevents energy loss due to leaks in ducts or refrigeration systems.
By understanding and optimizing the tightness rate, industries can enhance system performance, reduce risks, and comply with regulatory requirements.
Summary Table:
Aspect | Details |
---|---|
Definition | Measures how well a system prevents fluid leaks under pressure or vacuum. |
Importance | Critical for safety, environmental protection, and operational efficiency. |
Measurement Methods | Pressure decay, vacuum, bubble, and tracer gas testing. |
Factors Affecting | Material quality, design, assembly, and operating conditions. |
Applications | Pipelines, storage tanks, HVAC systems. |
Need help optimizing your system's tightness rate? Contact our experts today for tailored solutions!