The hardening process is a critical heat treatment method used to increase the hardness and strength of metals, particularly steel and cast iron. It involves three primary steps: heating the metal to a specific temperature, soaking it at that temperature for a predetermined time, and then rapidly cooling it. Each step plays a vital role in altering the metal's internal structure to achieve the desired mechanical properties. Additionally, specialized techniques like induction hardening allow for localized hardening, while processes like debinding are essential in removing binders from materials during production.
Key Points Explained:
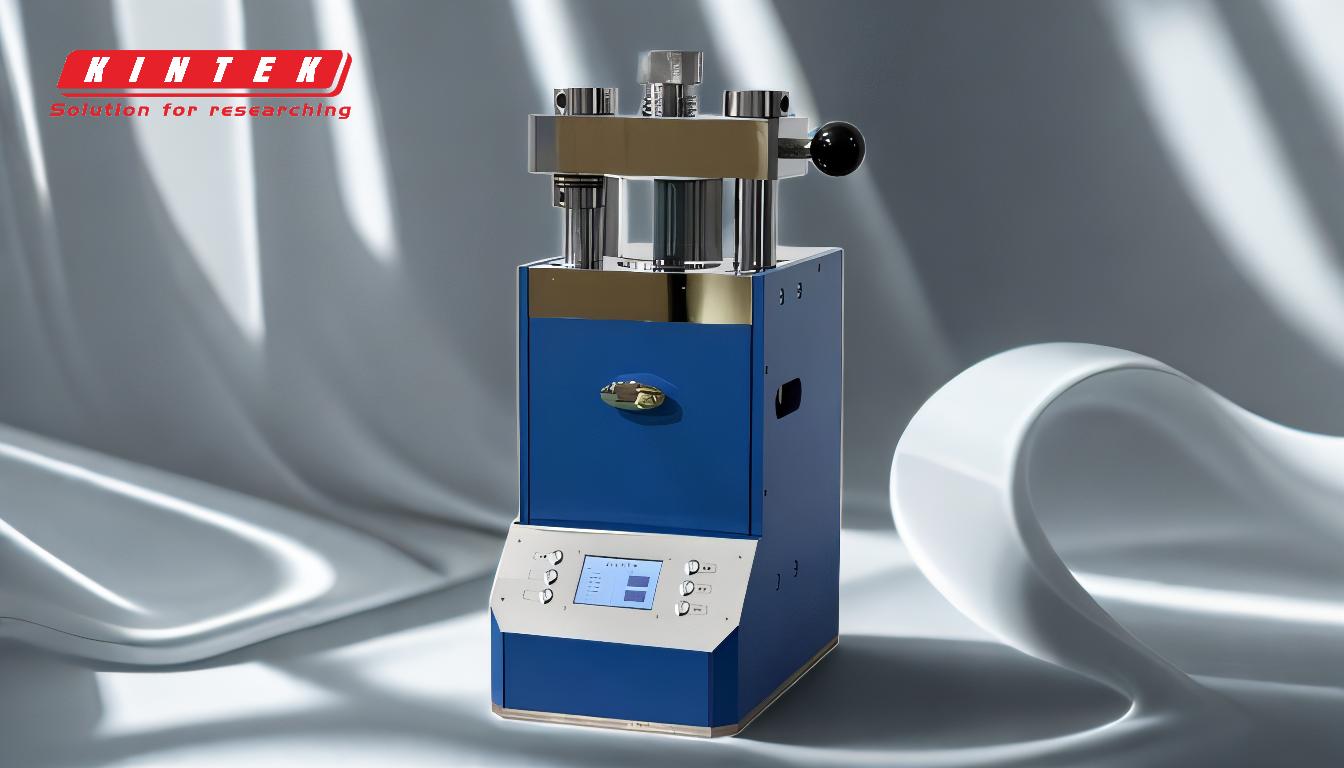
-
Heating the Metal:
- The first step in the hardening process is heating the metal to a specific temperature, typically above its critical transformation temperature. This temperature varies depending on the type of metal and its composition.
- Heating is done in a hardening furnace, which ensures uniform temperature distribution throughout the material.
- The purpose of heating is to transform the metal's internal structure into austenite, a high-temperature phase that allows for the rearrangement of atoms.
-
Soaking the Metal:
- After reaching the desired temperature, the metal is held at that temperature for a specific duration, known as the soaking time. This step ensures that the entire piece of metal achieves a uniform temperature and microstructure.
- The soaking time is typically calculated as one hour per inch of material thickness, ensuring complete transformation of the metal's internal structure.
- Soaking allows the metal to fully absorb the heat, which is crucial for achieving consistent hardness and strength.
-
Rapid Cooling (Quenching):
- The final step involves rapidly cooling the metal, usually by immersing it in a quenching medium such as water, oil, or air. This rapid cooling locks the metal's structure into a harder, more stable form.
- Quenching transforms the austenite into martensite, a hard and brittle crystalline structure that significantly increases the metal's hardness.
- The choice of quenching medium depends on the type of metal and the desired balance between hardness and brittleness.
-
Specialized Hardening Techniques:
- Induction Hardening: This method uses a high-frequency alternating current passed through a coil to induce rapid heating in specific areas of the metal. It is ideal for hardening localized sections without affecting the entire part.
- Debinding: While not directly part of the hardening process, debinding is a critical step in some manufacturing processes. It involves removing binders from materials using heat treatment or solvents, ensuring the material is ready for subsequent hardening or sintering.
-
Importance of Temperature Control:
- Precise temperature control is essential throughout the hardening process. Overheating can lead to grain growth, reducing the metal's strength, while insufficient heating may result in incomplete transformation.
- Modern furnaces and induction heating systems are equipped with advanced temperature monitoring and control mechanisms to ensure optimal results.
-
Applications of Hardening:
- Hardening is widely used in industries such as automotive, aerospace, and tool manufacturing to produce components with high wear resistance and durability.
- For example, gears, shafts, and cutting tools often undergo hardening to enhance their performance and lifespan.
By following these steps and understanding the underlying principles, manufacturers can effectively harden metals to meet specific performance requirements. Whether using traditional furnace heating or advanced techniques like induction hardening, the process remains a cornerstone of modern metallurgy.
Summary Table:
Step | Description | Purpose |
---|---|---|
Heating | Heat metal above its critical transformation temperature using a hardening furnace. | Transform internal structure into austenite for atom rearrangement. |
Soaking | Hold metal at the desired temperature for a specific duration (e.g., 1 hour/inch). | Ensure uniform temperature and microstructure for consistent hardness. |
Rapid Cooling | Quench metal in water, oil, or air to lock its structure into a harder form. | Transform austenite into martensite, increasing hardness and brittleness. |
Special Techniques | Induction hardening for localized heating; debinding for binder removal. | Achieve targeted hardening or prepare materials for further processing. |
Optimize your metal hardening process with expert guidance—contact us today!