Heat treatment is a critical process in metallurgy and material science, involving controlled heating and cooling of metals and alloys to achieve desired physical and mechanical properties. The primary requirements for heat treatment include precise temperature control, time management, and cooling rates to ensure the material attains the intended hardness, strength, toughness, and other characteristics. This process is essential for enhancing the performance of metals in industrial applications, as it modifies their microstructure and properties to meet specific operational demands.
Key Points Explained:
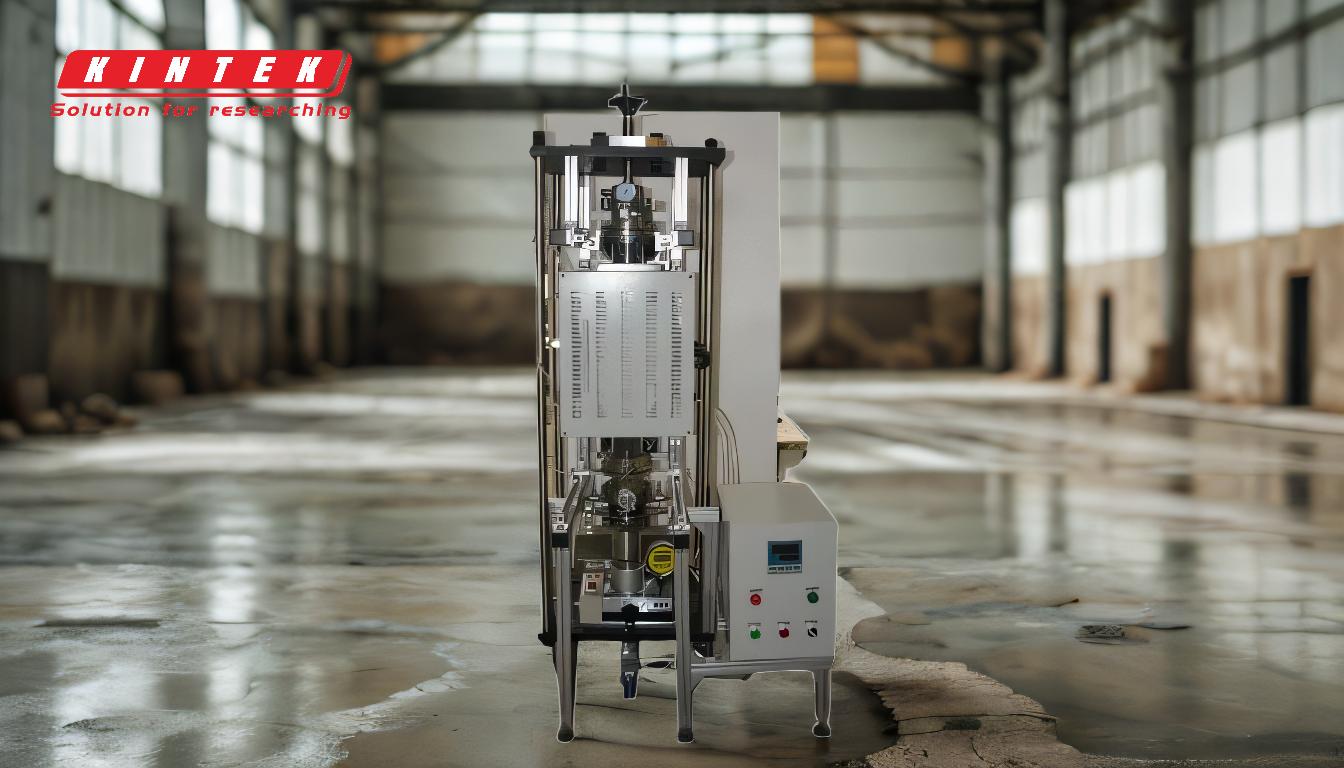
-
Definition and Purpose of Heat Treatment:
- Heat treatment involves controlled heating and cooling of metals and alloys in their solid state to alter their physical and mechanical properties.
- The primary purpose is to enhance properties such as hardness, strength, toughness, and wear resistance, making materials suitable for specific applications.
-
Key Requirements for Heat Treatment:
-
Temperature Control:
- Precise temperature regulation is crucial to achieve the desired microstructural changes.
- Different materials require specific temperature ranges to activate phase transformations or other metallurgical processes.
-
Time Management:
- The duration of heating (soaking time) must be carefully controlled to ensure uniform temperature distribution and complete transformation.
- Insufficient time can lead to incomplete treatment, while excessive time may cause undesirable grain growth.
-
Cooling Rate:
- The cooling rate determines the final microstructure and properties of the material.
- Rapid cooling (quenching) increases hardness but may reduce toughness, while slow cooling (annealing) enhances ductility and reduces internal stresses.
-
Temperature Control:
-
Types of Heat Treatment Processes:
-
Annealing:
- Involves heating the material to a specific temperature and then slowly cooling it to soften the metal, improve ductility, and relieve internal stresses.
-
Quenching:
- Rapid cooling from a high temperature to increase hardness and strength, often followed by tempering to reduce brittleness.
-
Tempering:
- Reheating quenched materials to a lower temperature to improve toughness and reduce brittleness while maintaining hardness.
-
Normalizing:
- Heating the material to a temperature above its critical range and then cooling it in air to refine the grain structure and improve mechanical properties.
-
Case Hardening:
- Surface treatment processes like carburizing or nitriding to increase surface hardness while maintaining a tough core.
-
Annealing:
-
Importance of Heat Treatment:
- Enhances the mechanical properties of metals, making them suitable for demanding industrial applications.
- Improves wear resistance, fatigue strength, and overall durability of components.
- Allows customization of material properties to meet specific operational requirements.
-
Applications of Heat Treatment:
- Widely used in industries such as automotive, aerospace, construction, and manufacturing.
- Essential for producing gears, shafts, bearings, cutting tools, and structural components.
-
Challenges and Considerations:
- Requires specialized equipment and expertise to ensure precise control over process parameters.
- Material selection and pre-treatment conditions must be carefully evaluated to achieve optimal results.
- Potential for defects such as cracking, warping, or uneven hardness if the process is not properly executed.
By understanding and implementing these requirements, heat treatment can significantly improve the performance and lifespan of metal components, ensuring they meet the rigorous demands of modern industrial applications.
Summary Table:
Aspect | Details |
---|---|
Temperature Control | Precise regulation to achieve desired microstructural changes. |
Time Management | Controlled heating duration for uniform transformation and grain structure. |
Cooling Rate | Determines final microstructure; rapid cooling increases hardness. |
Types of Processes | Annealing, quenching, tempering, normalizing, and case hardening. |
Applications | Automotive, aerospace, construction, and manufacturing industries. |
Challenges | Requires specialized equipment and expertise to avoid defects. |
Optimize your heat treatment process—contact our experts today for tailored solutions!